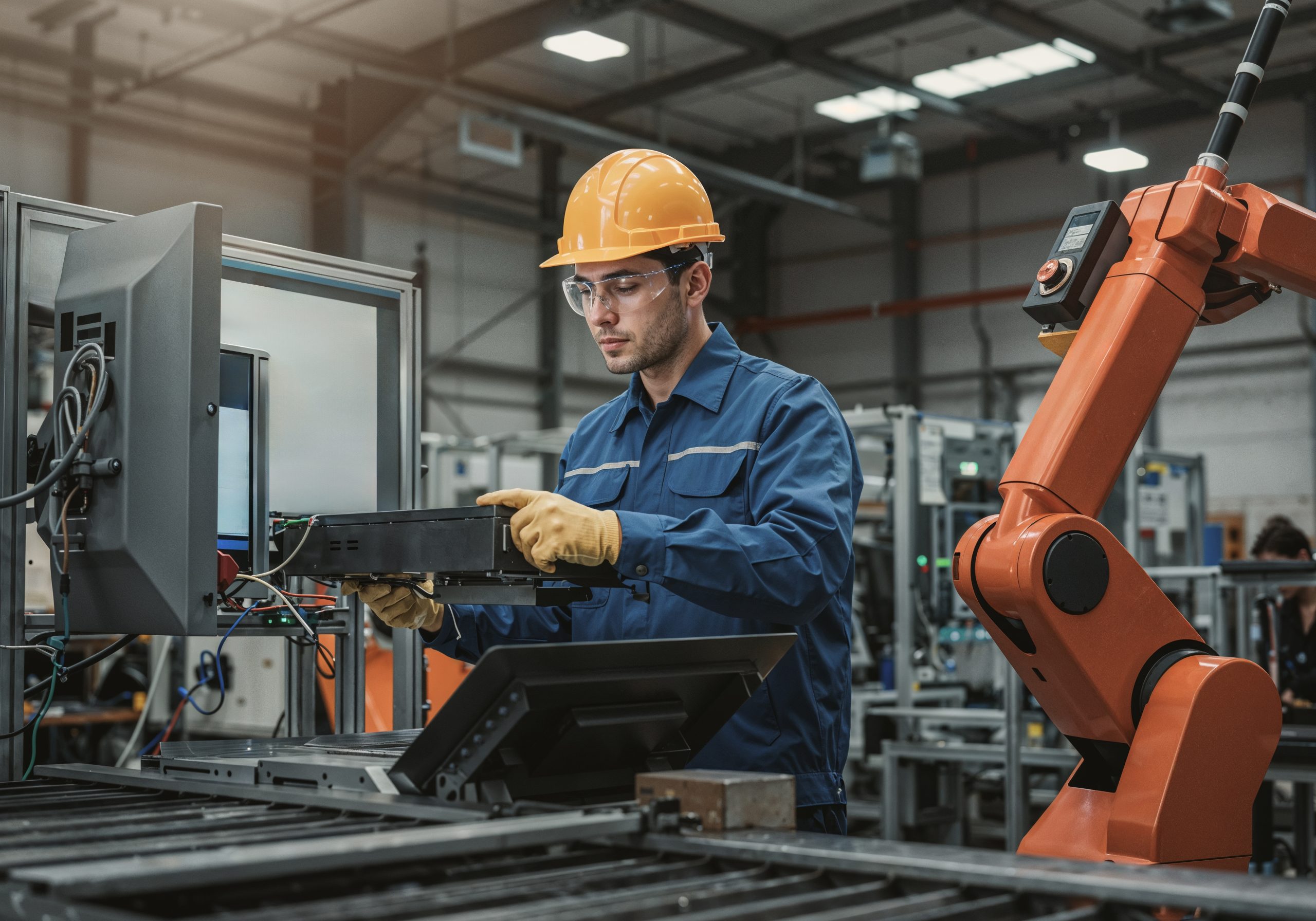
Overview
A leading manufacturing company with over 15 years of experience specializes in producing highly engineered composite patterns, molds, and components for OEMs in industries such as wind energy, mass transportation, and industrial equipment. Known for its product excellence, process innovation, speed to market, and customer service, the company has grown into a major player in the composites sector. It employs over 1800 professionals and operates multiple manufacturing facilities across the country.
- Industry Manufacturing
- ERP Solution SAP Business One Implementation
Challenges Before SAP Business One Implementation
Prior to implementing SAP Business One, the company relied on legacy systems and Excel-based tools to manage critical operations, which led to several business challenges:
Business Benefits After SAP Business One Implementation
- Centralized procurement approval workflow for better control
- Systematic in-ward quality inspection based on item-specific parameters
- Automated QC Quarantine Warehouse handling and reporting
- Custom-built returnable and non-returnable material tracking
- Optimized purchase management through a dedicated procurement management tool
- Improved SKU tracking and inventory accuracy across all branches
- Automation for minimum and maximum stock level alerts
- A semi-customized production module for tracking WIP, returns, scrap, and final product costs
- BOM vs. actual consumption cost analysis for production optimization
- Integrated resource cost tracking to support accurate customer quotations
- A structured sales budget module to compare estimated vs. actual expenses
- Final quality control through automated inspection and quarantine processes
- Better sales order handling and dispatch planning
- Enhanced customer service and delivery fulfillment
- All business operations consolidated within a single ERP platform
The Solution
The company was seeking a scalable, centralized ERP system that could unify business operations across its multiple units. SAP Business One was identified as the ideal fit and successfully implemented by an experienced ERP partner. The solution was customized to accommodate unique workflows and industry-specific challenges, enabling real-time data access, better inventory control, and integrated process management across departments.